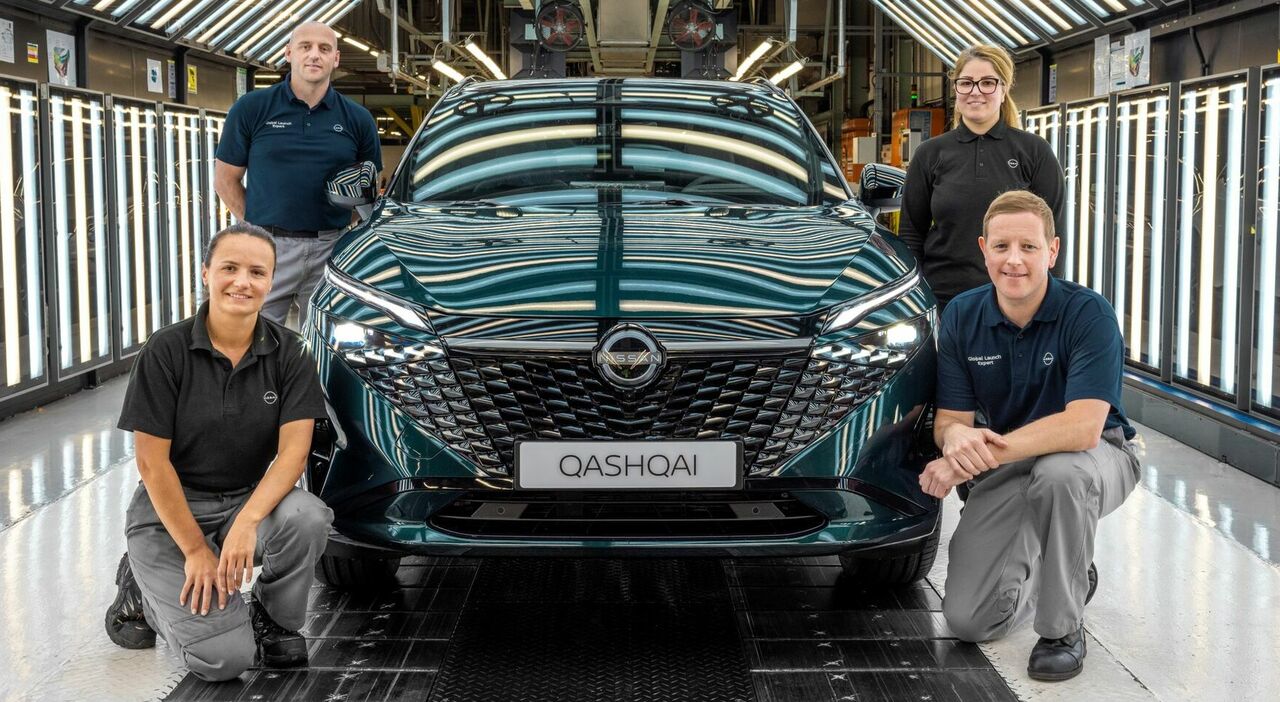
Vince la formula Nissan: giapponesi d’Inghilterra. Rinnovato l’impianto di Sunderland dove il brand dal 1986 ha investito 6 mld di sterline
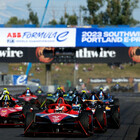
A Portland il penultimo appuntamento della 10^ stagione. Due EPrix nel weekend, l'anno prossimo si torna a Miami

Vince la formula Nissan: giapponesi d’Inghilterra. Rinnovato l’impianto di Sunderland dove il brand dal 1986 ha investito 6 mld di sterline
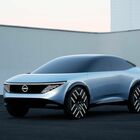
Nissan Leaf diventa un Suv per la sua terza generazione. Potrebbero prendere ispirazione dal concept Chill-Out
Nella complessa dialettica tra il Governo italiano e i costruttori di auto per la costruzione di impianti produttivi nel nostro Paese, proponiamo un viaggio di lavoro in Inghilterra. Precisamente a Sunderland, 200.000 abitanti a pochi chilometri da Newcastle, nord est del Regno Unito al confine con la Scozia e a una settantina di chilometri dal luogo dove l’Imperatore Adriano fece costruire il mitico Vallo, la fortificazione in pietra che impedì per un po’ ai barbari locali di invadere la Britannia controllata dall’Aquila di Roma. Ecco, un viaggetto da queste parti sarebbe istruttivo. Perché qui, 38 anni fa è stata costruita una fabbrica diventata modello industriale e produttivo per l’Europa e non solo. Tutto grazie a un costruttore straniero, la Nissan e, praticamente, a un solo modello (o quasi): la Qashqai. Questo, in un Paese dove almeno un certo tipo di nazionalismo è andato a farsi necessariamente benedire da tempo, a giudicare dalle proprietà dei gioielli motoristici della... Corona. Con Land Rover/Jaguar degli indiani di Tata, la MG dei cinesi, Bentley, Mini e Rolls Royce dei tedeschi.
A noi hanno fatto visitare il sito produttivo di Sunderland per festeggiare l’avvio della produzione della terza generazione di Nissan Qashqai e abbiamo capito tante cose. Ma prima cominciamo con i numeri. Più di 6.000 dipendenti, oltre i 30.000 dell’indotto. Tre milioni di metri quadrati dove oggi si producono 300.000 vetture all’anno, ma il potenziale è di 500.000, cioè un’auto ogni 2 minuti. Sono attive due linee produttive: una per la Qashqai di terza generazione e-Power e l’altra per Juke e Qashqai. La prima linea impiega 14 ore per realizzare un’unità, la seconda 24 ore. Una storia, quella dello stabilimento di Sunderland, iniziata appunto nel 1986 con la prima vettura assemblata, la Blubird; decollata nel 1992 con la Micra per poi essere trasformata in autentica macchina da guerra con la Qashqai di cui il sito inglese dal 2006 ha prodotto tutti i 4,4 milioni di pezzi (120.000 e-Power). Parliamo del 20% dell’intera produzione automobilstica del Regno Unito negli ultimi 18 anni... Con Juke a 1,4 milioni e le Leaf a 282.000 pezzi. Ma una storia non si può fondare sul nulla.
Perché l’orgoglio dei lavoratori di Sunderland è figlio di investimenti importanti da parte di Nissan che qui ha messo sul tavolo qualcosa come 6 miliardi di sterline, compreso l’ultimo, il più recente che servirà a evolvere Sunderland in chiave ancora più elettrica. Coerente con la pianificazione Nissan denominata EV36Zero che prevede dal 2030 in Europa solo produzione elettrica con il passaggio intermedio del 2026 dove la quota dovrà arrivare al 40% con i 16 nuovi modelli elettrificati in arrivo (8 tutti elettrici tra cui Juke su base del concept Hyper Punk, Qashqai su quello HyperUrban e la Leaf sul prototipo Chill Out del 2021). Ma sono previsti anche 14 modelli a combustione. La sostenibilità comunque da sempre è uno dei pilastri di Sunderland. Con i due parchi fotovoltaici presenti all’interno dell’area - uno da 5 MW del 2016 e uno da 20 MW più recente - oltre alle 10 pale eoliche da 6,6 MW. La somma produce il 20% dell’energia necessaria allo stabilimento, e ne è previsto un terzo da 7,5 MW estendibile a 35 MW. Ma è tutta la produzione dello stabilimento ad essere fondata sull’economia circolare, avendo innescato un circuito virtuoso per il recupera di tutti gli scarti di alluminio, acciaio, plastica, addirittura vernice e legno.
Un’organizzazione razionale e ordinata che comincia dall’impressionante impianto dello stampaggio, il primo della storia che trasforma bobine di acciaio da 13 tonnellate insieme a pannelli di alluminio per una riduzione di peso di 60 kg e opera tagli con tolleranza di 0,1 mm, per poi passare all’assemblaggio dei pacchi batterie (40’ a pacco, per 49 operazioni: in tutto 640 al giorno). Al body shop si assembla la scocca con 1.000 robot. Lo step successivo è la verniciatura dove un sofisticato sistema di aspirazione recupera tutta la vernice dispersa dei 5 litri necessari per “colorare” una vettura. Al resto pensa l’assemblaggio di motori, interni e cristalli. Insomma, uno spettacolo autentico, dove in realtà “pesa” anche la mano del Governo inglese e dell’amministrazione locale che hanno supportato Nissan con circa 1 miliardo di sterline. Anche se l’ottimizzazione della catena di approvvigionamento è il vero segreto della riduzione dei costi. Con fornitori tutti locali, comprese le batterie che arrivano da una Gigafactory da 1 gWh vicino Sunderland di proprietà dei cinesi di AESC. Tutti motivi in più per un viaggio di... studio.