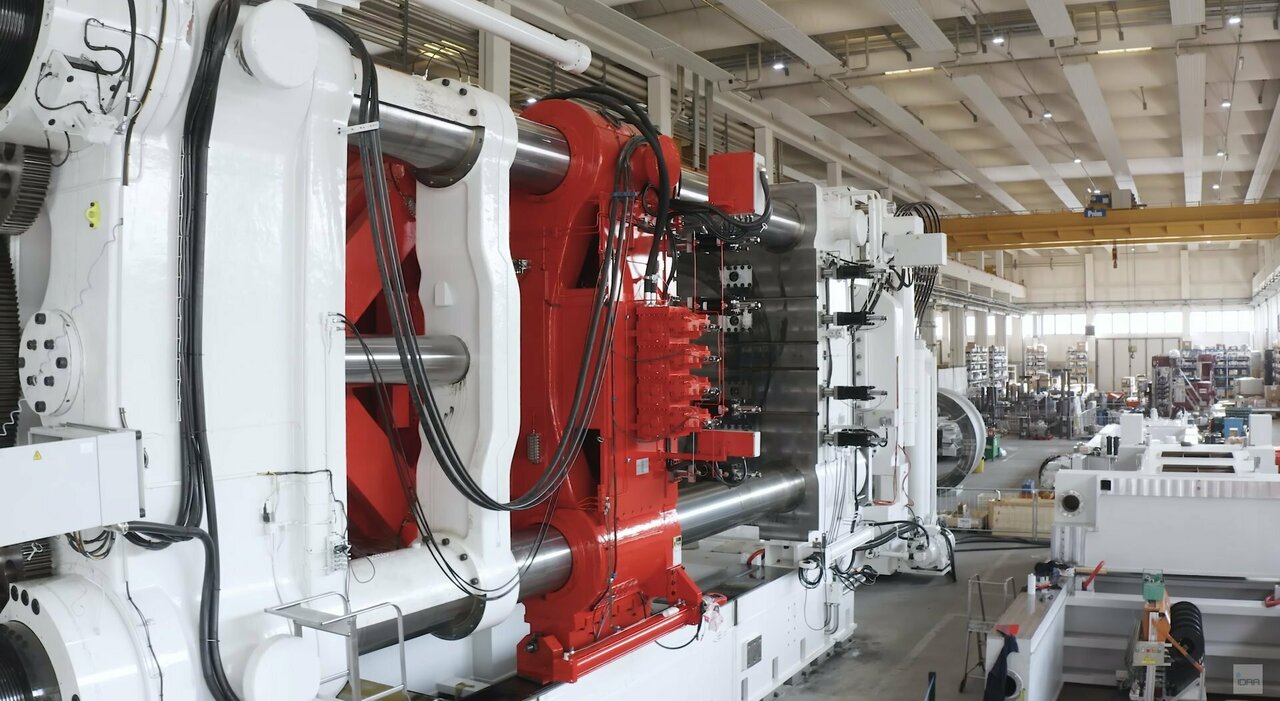
Tesla, ecco le gigapresse che stampano il pianale intero di una vettura dimezzando i costi di produzione
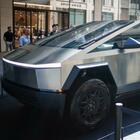
Tesla Cybertruck arriva in Europa. Debutto italiano al Motor Valley Fest di Modena
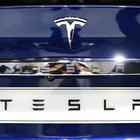
Tesla, vola a +12% a Wall Street dopo via libera a guida autonoma in Cina
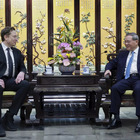
Tesla, Musk termina visita a Pechino dopo intesa su sicurezza dati. Trattative anche per via libera a guida assistita
Tesla starebbe studiando un nuovo processo produttivo che permetterebbe di ricavare la parte inferiore completa delle sue future vetture in un unico pezzo grazie a gigapresse, utilizzando la stessa filosofia già applicata per realizzare la parte anteriore e posteriore delle Model 3 e Model Y. Tale innovazione permetterebbe di ridurre i pezzi necessari da 400 ad uno e di abbattere il costo di produzione di un componente fondamentale e dunque offrire al mercato un prodotto finale con un prezzo inferiore ai 25.000 dollari con profitti maggiori. In questo modo, Tesla conta entro il 2030 di vendere 20 milioni di automobili all’anno dimezzando il costo industriale per unità.
Lo sostiene l’agenzia Reuters che ha raccolto la testimonianza di cinque persone anonime le quali stanno lavorando al progetto che dovrebbe trovare applicazione sui due modelli cruciali per i piani di sviluppo già presentati da Elon Musk lo scorso marzo: la piccola (Model 2) e il robotaxi a guida autonoma. Il nuovo procedimento che Tesla sta mettendo a punto sarebbe ancora più sofisticato e sfidante rispetto a quello già esistente e avrebbe bisogno di presse giganti, da almeno 16.000 tonnellate, ancora di più di quelle da 6.000 e 9.000 tonnellate che vengono già utilizzate per la parte anteriore e posteriore della scocca e che Tesla, come è ormai è noto, acquista dalla Idra, azienda di Travagliato (BS) assurta alle cronache mondiali proprio per i suoi macchinari e il suo illustre committente.
Il nuovo processo permetterebbe, come raccontato dagli insider, di portare il cosiddetto time-to-market (lo sviluppo di una vettura dalle prime fasi fino alla sua commercializzazione) a 18-24 mesi rispetto ai 36-48 mesi oggi necessari, dunque dimezzando anche i tempi di sviluppo ed industrializzazione. Tuttavia le sfide tecnologiche non sono poche perché ricavare un solo pezzo così complesso e con una sola operazione non è cosa semplice e ha avuto bisogno di prove e investigazioni che hanno portato a rivedere i metodi di fusione dello stampo stesso, la tipologia dell’alluminio impiegato e le modalità in cui il metallo deve essere introdotto all’interno della pressa in modo che il pezzo sia stampato ricavando le sagome e le pieghe necessarie ad assicurare tutte le caratteristiche funzionali, torsionali e di resistenza in caso di incidente.
La prima sfida è ricavare lo stampo, metterlo a punto nei particolari ed eventualmente modificarlo per migliorare i livelli di qualità o per implementare una variazione. Con i metodi attuali, gli esperti interpellati da Reuters, parlano di 100.000 dollari per ogni stampo di prova e, nel caso sia rifare lo stampo definitivo di 1,5 milioni e, se ci si trova a dover rifare da capo una pressa di grandi dimensioni, ci vogliono 4 milioni. Per risolvere questo problema Tesla si sarebbe indirizzata verso una metodologia che prevede per gli stampi di prova della stampa 3D partendo da un file digitale, attraverso l’applicazione graduale di strati di materiale e sabbia, ampiamente usata per processi di fusione per colata. I questo modo i costi di prototipazione dello stampo definitivo diventerebbero solo il 3% di quelli tradizionali.
Se davvero così fosse, fare uno stampo prototipale avrebbe bisogno di una spesa infinitamente inferiore e di tempi nettamente più brevi: la stampa di un prototipo avrebbe bisogno di poche ore e l’intero processo, dalla progettazione fino alla fusione dello stampo definitivo, calerebbe da 6-12 mesi a 2-3 mesi. L’altra sfida è sagomare in un colpo solo un componente di grandi dimensioni, altamente complesso e differenziato e che deve avere un peso contenuto il più possibile. Le zone preposte ad ospitare la batteria deve avere infatti caratteristiche ben diverse da quelle dei sottotelai delle sospensioni e dalle zone di assorbimento degli urti. Per fare questo, ad oggi, un pianale ha bisogno di circa 400 pezzi utilizzando materiali, metodologie di formatura e di metallurgia diverse che richiedono tempi differenziati e metodi di giunzione (saldatura, incollatura, rivettatura…) standardizzati.
Per superare questo scoglio, Tesla avrebbe studiato un metodo di pressatura dell’alluminio assai complesso utilizzando leghe speciali trattando il pezzo con metodi di raffreddamento di post-trattamento termico che permetterebbero di ricavare zone con caratteristiche differenziate. Infine, per ricavare forme complesse, come le cavità di alleggerimento, queste presse provvederebbero ad iniettare il metallo fuso al loro interno lentamente. Sarebbe un rallentamento che, alla luce dei miglioramenti acquisiti, risulterebbe altamente tollerabile e non comprometterebbe la grande accelerazione globale data alla produttività. L’implementazione di queste giga presse e di questi metodi sarebbe facilitata dal fatto che interesserebbero vetture di dimensioni inferiori a quelle delle Tesla attuali e che hanno bisogno di un pianale più piccolo, con sbalzi e passo inferiori, e meno complesso.
Resta dunque da vedere se la Model S o la Model 3 del futuro potranno beneficiarne. Secondo le fonti di Reuters, il nuovo processo è stato già messo a punto ed entro la fine del mese si deciderà se implementarlo. Il passo, oltre ad implicare investimenti, comporterà anche una rivisitazione degli stabilimenti viste le già enormi dimensioni dei locali richieste dalle gigapresse la cui potenza è destinata quasi a raddoppiare. In questo modo il pianale di una vettura diventerà «in un certo senso come una barca, un vassoio per la batteria con piccoli ali attaccate agli estremi», come dichiarato dai tecnici interpellati.
ACCEDI AL Il Gazzettino.it
oppure usa i dati del tuo account